Article Contents:
Why is holistic measurement (OEE)required to understand operational performance?
You know the famous quote, “What you measure is what you get.”
Measuring is significant for business performance, and what and how you measure are critical. If you measure wrong, suboptimal, or standalone objective, then your business performance will also be suboptimal.
For example,
Typically, we measure our business or plant in the following ways.
1. Utilization perspective :
In this measurement, we measure how many hours plant is running against total available time. For example, if plant runs for 6 hours against total shift hours, say 8 hours, we measure plant utilization is 75 %.
It is straightforward, however, it will not indicate any other people efficiency or product quality performance.
2. Efficiency perspective :
In this measurement, we measure the people’s efficiency as how much people produced against the standard qty. For example, if the shift standard output is 1000 pieces and in a particular shift, people produced only 800 pieces , we declare plant efficiency as 80%.
It gives more focus on the quantity against standard, however, it does not indicate the utilization losses and quality output .
3.Capacity Perspective:
In this measurement, we measure the plant effectiveness against installed capacity. For example, plant has capacity to produce 2000 T and the actual production is 1000 T, we say capacity utilization as 50 %.
As mentioned earlier, it does not bring out the utilization losses or even efficiency losses. Every losses are combined together and there is no scope for further analysis or improvement.
In some organization, people use to measure the revenue they generated against the machine hour rate. For example, machine hour rate is Rs 1000 and the revenue generated is Rs 600, then plant effectiveness is 60 %.
Machine hour rate is dynamic and it will vary from organization to organization and small companies do not have bandwidth to calculate the machine hour rate frequently and also this measurement does not reveal the reason for utilization , efficiency losses.
5.Yield Performance perspective:
Some organizations use the yield indicator as a performance measure.
All those measures are right and serve the purpose to some extent for what it is intended. For example, you may measure capacity utilization as the ratio of production qty/capacity installed, which measures, say, 80 %; that means you may conclude that 80 % of the installed capacity is utilized. It may not give other information like the efficiency during the production and how much actively passed through quality specification how much cost you incurred and so on.
Likewise, all the above typical measurements will give you standalone, suboptimal information about each function, which you need to consider together to arrive at some common conclusion about your overall business or plant performance.
To overcome the above limitations only, smart organizations adopt one measure, which will give a holistic view of your plant or business effectiveness rather than standalone performance or utilization or yield performance.
The metric of OEE (Overall Equipment Effectiveness) fills the gap.
Introduction to Overall Equipment Effectiveness :
OPE(Overall Plant Effectiveness):
If your plant is small, one or a few assembly lines determine your business profitability. You can measure that assembly line, which will directly correlate with your business performance. You can measure it as Overall Plant Effectiveness.
OEE( Overall Equipment Effectiveness):
If your plant is relatively large and consists of many equipment and assembly lines, you can identify the most critical or constrained equipment and measure it holistically. There, you can measure the Overall Equipment Effectiveness.
If we apply OPE or OEE correctly in a small, emerging organization, this will directly correlate with delivery performance, sales turnover, and profitability, as I have seen in my client organizations, irrespective of their manufacturing industry classification.
The measure, either OPE or OEE, will consider the importance of EFFECTIVENESS rather than any standalone measure like efficiency, utilization, or yield performance.
What is meant by OEE?
Overall Equipment Effectiveness (OEE) is one of the proven and best METRICs used for monitoring and improving the Efficiency of manufacturing processes.
The manufacturing processes can be machining, fabrication, powder coating, and assembly line.
OEE is a simple, holistic, and powerful metric.
OEE takes into account the typical sources of manufacturing productivity losses and groups them into three categories: availability, performance, and quality.
Grouping them into different categories distills the complex manufacturing losses into simple metrics.
It helps us understand the losses clearly and choose the right lean tool for each loss. In addition, it helps us verify the effectiveness of each action against each manufacturing productivity loss.
Benefits of OEE measurement:
- As this measure encompasses utilization, efficiency, and quality performance, you will get a holistic idea of your plant’s effectiveness at the end of the day rather than other measures like utilization, plan vs actual, efficiency, etc
- Easy to communicate to all FUNCTIONS
- Since all functions involved in the improvement of this measure, this measure enhances engagement among people, as I witnessed in my client’s operations
- Helps to focus on the overall performance of the plant rather than standalone areas
- It has a direct correlation with increase in capacity, delivery volumes, sales turnover and profitability if properly administered
Elements of OEE measurements
It consists of 3 parts: Plant Utilization, Output efficiency, and product yield performance.
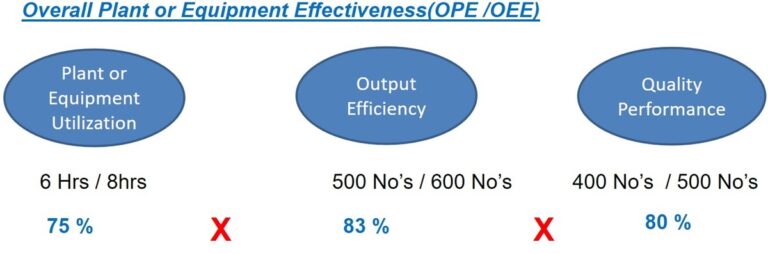
In the picture above,
The plant utilization is given as 75 % as it is derived from the ratio of working hours ( 6 hours) to available hours ( 8hours)
The output efficiency is given as 83 % as it is derived from utilization data.
For example, in a given 6 hours, the plant supposes to deliver 600 pieces ( assume 100 per hour), whereas, the plant produces the actual output as 500 pieces. hence plant efficiency is 500 / 600 equals to 83 %
The quality performance is given as 80 % as it is derived from efficiency data, For example, 500 pieces produced and 400 pieces only pass through the quality test, and the final yield is 400/ 500 equal to 80 %
Hence, Overall Plant Effectiveness (OPE) is a multiplication of Plant Utilization and Output efficiency and Yield improvement.
That is 49 %
So, instead of looking at standalone measure either 75 % plant utilization or 83% people or output efficiency or 80 % yield performance, you get a HOLISTIC MEASUREMENT to say EFFECTIVENESS as 49 %.
This measure will give you a HOLISTIC idea about your plant’s Effectiveness at the end of the day.
Business Implication of EFFECTIVENESS measure:

what does 49 % OPE or OEE indicate?
Given your current sales turnover or profitability, whatever you achieve is due to operating the plant at 49 % effectiveness. If you want to improve sales turnover or profitability, it is only possible by enhancing plant effectiveness measures. Improvement of plant effectiveness measures can be working on plant utilization losses, people efficiency losses, and improving quality issues.
The action point is to understand your current plant or equipment effectiveness and the reason for the losses and the improvement actions to improve the Effectiveness and, in turn, your business performance.
How to calculate OEE ?
As mentioned, OEE is calculated from three categories: availability, performance, and quality.
OEE = Availability * Performance * Quality
Pl note that OEE is not calculated as an addition or average of three categories; it is calculated by multiplying three categories.
For example
Availability = 75 %
Performance =90 %
Quality = 89 %,
Then
OEE= 75 % * 89 % * 90%
= 60 %
Availability Calculation:
Availability is the ratio of actual operating time to planned operating time.
It measures the downtime loss.
Availability = Operating Time / Planned Available Time
Operating time = Planned available time – downtime loss
For example
Availability =Actual Operating Time (300 min) / Planned Operating Time (400 min)
=75 %
Planned operating time:
For example, you are running a shift for 8 hours
Planned Available time per shift is 8 hours or 8 * 60 = 480 min
Note :
In some organizations, it is a practice to shut down the equipment for morning meetings, refresh breaks, lunch breaks, etc. within 8 hours. In that case, you can deduct those times from the planned available time straightaway.
For example,
Morning meeting – 10 min
Lunch break – 30 min
Refresh break – 20 min
Scheduled maintenance check – 10 min
Hence planned shutdown time = 10 + 30+20+ 10=70 min
Hence, the planned operating time is 480 -70 = 410 min
Actual Operating Time
Planned Available time – down time
=410 – 110*
=300 min
*Break up of downtime (110 min ) can be
Machine breakdown -20 min
Operator not available – 30 min
Material not available – 10 min
Changeover loss – 50 min
Hence,
Availability = actual operating time / planned operating time
=300/ 410
= 73 %
Performance:
Performance is the ratio of the actual quantity produced during operating time to the standard quantity that can be produced during operating time.
From the above example,
Actual operating time = 300 min
Say std time per piece = 3 min
So standard output can be produced or expected during operating time = 300/3 =100 pieces
Suppose, in a given actual operating time, the actual qty produced is 270 pieces, then
Performance = 270 / 300
=90 %
Quality:
Quality is the ratio of good quantity produced to total quantity produced.
From the above example,
Total quantity produced = 270 pieces
Good quantity = 240 pieces
Rejection / Rework quantity = 30 pieces
Hence,
Quality = 240 / 270
=89 %
After calculating all three elements, we can arrive at OEE % by multiplying the three values.
From the same above examples.
Availability: 73 %
Performance: 90 %
Quality: 89 %
Hence OEE would be = 73 % * 90 % * 89 % = 58.47 %
How much OEE % is considered as GOOD for discrete manufacturing process?
Generally, world-class OEE for discrete manufacturing processes is considered 85 % or greater than 85 %
It is arrived from Availability (90 %) * Performance (95%) * Quality (100 %) = 85 %
The study generally indicates that the average OEE score for the discrete manufacturing process is around 60 %.If we aim for an excellent OEE standard of 85 %, then we can realize that there is much opportunity to move from 60 % to 85 % through loss elimination or reduction initiatives.
As a business head, you can always aim to increase the OEE % as high as possible. However, we should minimum strive to achieve 85 % OEE in a discrete manufacturing process.
In my experience, many companies in small, emerging spaces find it difficult to achieve that level, which indicates that potential for waste exists in the system, and we need to encourage the team to eliminate or reduce the waste as much as possible to achieve a consistent 85 % OEE.
Can we apply the OEE concept in other than manufacturing functions?
Yes. We can apply the concept of OEE in any function beyond manufacturing. It is widely used in the manufacturing environment as the impact of losses on the organization is high.
For example, realizing the potential of OEE measurement in driving business results in a manufacturing environment, one of my clients asked me to apply the OEE concept in an office environment, say, the Finance function, as most of them felt there was scope for improving the finance function’s effectiveness.
First, we need to understand the purpose of administering OEE in any function. The purpose is not to find fault with the people by measuring efficiency and utilization. The main purpose is to identify the major losses that affect the function and other functions in the organization.
By properly modifying the OEE format, we gathered many losses, and we could see some patterns of repetition.
For example, staff in the finance function used to wait to get signatures from higher officials before uploading the travel bills and also getting approval for paying the travel reimbursement to the employees. From a lean perspective, the activity of getting approval before uploading the bills into the system is a waste, and also it is a duplication. The higher official does not add any value in signing the bills before uploading. That can be delegated to the staff and the higher official will have control while approving the reimbursement bill. Hence the activity of waiting for approval was eliminated.
Also, the uploading of bills was assigned to respective functions, and the activity of uploading was also eliminated.
The idea of administrating OEE in the office function is to identify waste and look for improvements to eliminate or reduce it through automation, policy changes, avoiding duplication, etc.
By implementing some of the process changes in the finance function, the effectiveness is improved by 38 %
Hence, OEE can be administrated in any function other than manufacturing, and we need to look for a waste pattern from OEE data collection.
Steps in Implementing OEE measurement Process
- Identify the facility or equipment or line to be measured
- Understand the current OEE level approximately
- Collect shift wise/day-wise data for specified period
- Identify the loss pattern
- Classify the losses in each category
- Prioritize the losses
- Choose the right lean tool for elimination or reduction of losses
- Make an action plan to improve the OEE score by addressing the losses
- Implement the solution and monitor the OEE trend and losses trend
- Correlate increase in OEE with increase in plant delivery or capacity
- Continue the above steps
Sample format for collecting OEE data in small business
Given below the sample for at for collecting the losses in the machine shift wise and day wise.
The parameter can be changed according to your losses.
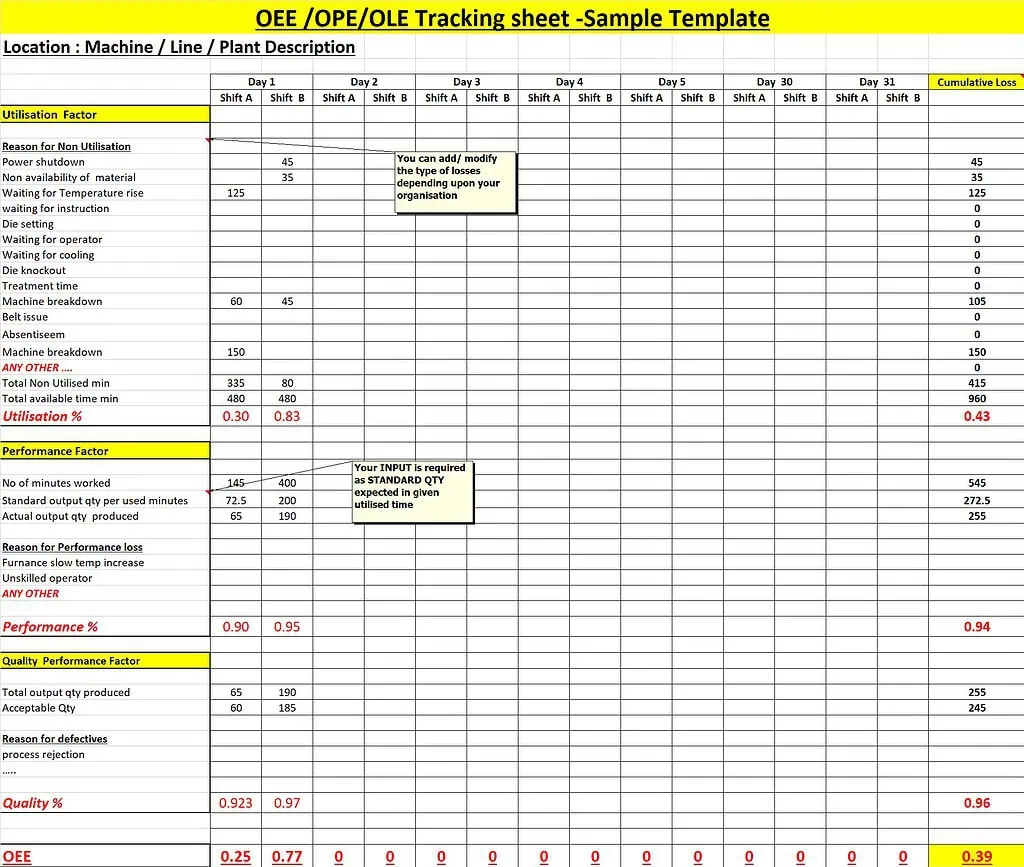
Real case study examples of OEE Impact on Business profitability
Given below the real example of OEE measurement implementation to eliminate waste in the system and its impact of sales turnover and manufacturing cost reduction in one of my client’s organization. For confidential reasons, actual figures was not shown, however, the correlation data were right.
OEE is being used as one of the KPI of the business.
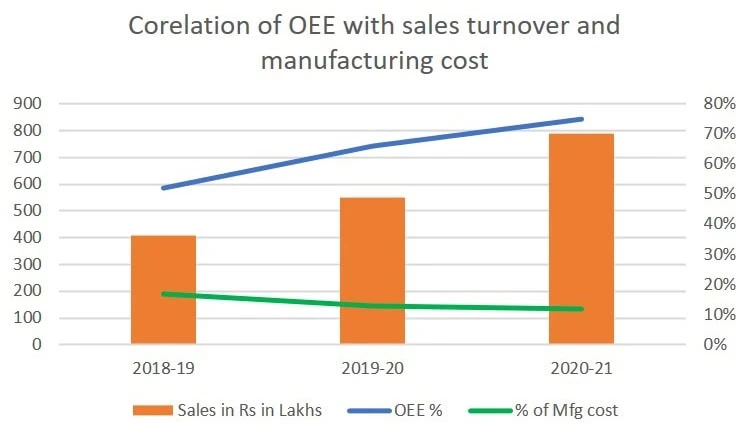
Summary
Implementing the OEE measurement in a small organization will have more impact than large organization thanks to a few critical processes which will have direct impact on delivery, sales and profitability
CEO and leadership team play a vital role in inculcating the right measurement system