Article Contents:
What is Inventory Management in small business?
Controlling the flow of materials is a crucial aspect of inventory management.
It is all about managing inventory movements and quantity to meet the customer’s demand on time while minimizing the costs associated with holding inventory.
Inventory management is all about
- what items are to be kept in inventory
- how much inventory to hold
- when to order
Inventory management is applicable at all stages of material movement in the business, viz RM ( Raw Material) + WIP (work in progress)+ FG ( Finished goods).
In the RM stage, materials are further classified into direct materials, which are used in products like castings, sheet metal, paper, etc., and Indirect materials, which are required for manufacturing products like consumables, spares, etc.
Hence, Inventory Management is all about managing the right inventory to balance the demand and cost at all stages of materials movement in the value chain.
Elements of Inventory Management
Effective inventory management involves managing various sub-activities to optimize inventory levels according to customer demand while minimizing costs.
The following are the sub-activities:
- Sales forecasting: This involves estimating the amount of a product required over a specific period, usually the next three months. Sales forecasting can be based on past demand data, market trends, judgment, and customer feedback.
- Ordering and purchasing: This sub-activity involves determining when and how much to reorder products based on factors such as consumption patterns, lead time, and minimum order quantity (MOQ) conditions.
- Receiving and storing: This involves receiving shipments from vendors, inspecting them for quality and accuracy, and storing them in the warehouse or storage facility.
- Tracking and monitoring: This involves keeping accurate records of inventory levels, movements, and locations using inventory management software or manual systems.
- Inventory valuation: This sub-activity involves assigning a value to the inventory on hand for financial reporting purposes, typically using methods such as FIFO (First In, First Out) or LIFO (Last In, First Out).
- Inventory optimization: This sub-activity involves analyzing inventory data to identify inefficiencies and opportunities for improvement, such as reducing stockouts, minimizing excess inventory, and optimizing inventory turnover.
Is Inventory Good or Bad for small business?
It is difficult to say whether inventory is always beneficial or detrimental to a business.
However, maintaining inventory, whether in the form of raw materials or finished goods, can help to manage uncertainties on both the supply and demand side. These uncertainties may arise due to inaccurate sales forecasts, delays in the supply of raw materials, fluctuations in commodity prices, and other factors that are typically beyond the control of the business.
However, maintaining high inventory levels in anticipation of high sales forecasts or as a precautionary measure to manage risks can result in tying up a significant amount of capital that could otherwise be used for other business expenses.
Therefore, whether inventory is good or bad for a business depends on the specific context of the business.
The following benefits are realized after implementing some of the waste elimination techniques involving key members in production and support areas.
Delivery performance improved to 92%
Turnover increase by 3 times within 12 months time
No of shifts reduced from 3 to 1
Rejection reduced to 2 % from 10 %
Changeover time reduced from 6 hrs to 30 min
OEE improved to 65 %
Inventory was reduced by 54 % even with increase in turnover by 3 times
The benefits of lean system thinking in small manufacturing businesses are huge, and they can be made possible with an engaged team, a senior leadership team, and, of course, an experienced expert.
Typically, you can see benefits in the following areas
- Inventory reduction
- Lead time improvement
- Rejection reduction
- Enhancement in people engagement
- Increase in the confidence of the team towards business challenges
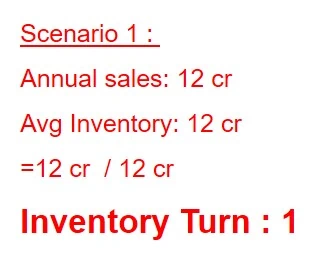
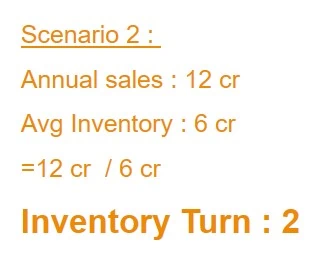
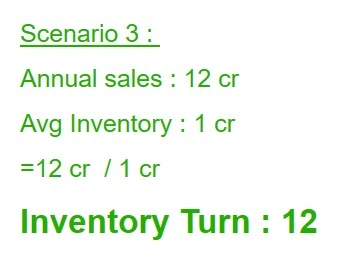
By having 12 cr worth of inventory, you manage to make 12 cr sales turnover.
That means you need working capital at any point of time is 12 cr
In this scenario, by having 6 cr inventory on hand, you able to make turnover of 12 cr.
That means you need only 6 cr worth of working capital which you can rotate 2 time in a year
.In this scenario, by having 1 cr inventory, you able to make turnover of 12 cr.
That means you need only 1 cr working capital and you can rotate 12 times in a year.
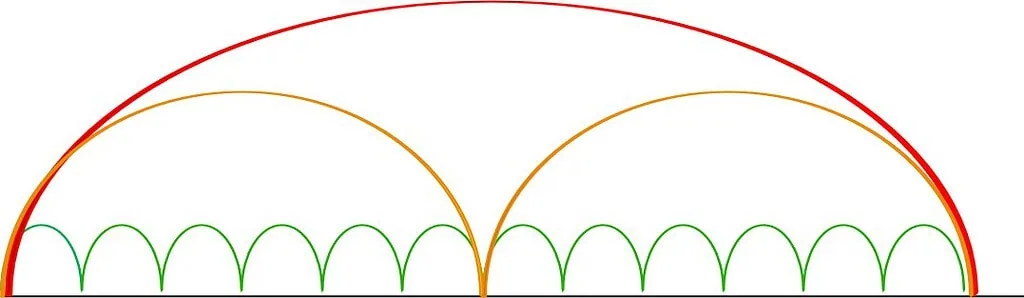
In all the scenarios, which is better for the business in terms of cashflow requirements?
Scenario 3 requires less inventory, and the cash is rotated 12 times in the year.
Higher the Inventory Turn, Better the cash flow
Operational Impact:
More you have high inventory, more you will have operational difficulties like
- Storage / Floor space
- Handling
- Manpower
- Communication
- Planning
- Quality issues
How to measure Inventory and set target?
One of the questions most of the business head used to ask is,
” How do I know my inventory level is high or low? How can I measure Inventory and I track? What is the benchmark for the inventory level?
My answer would be as follows.
Comparing or benchmarking may not give the right approach.
As we mentioned in Holistic approach to manage inventory in small organizations, Inventory is a function of many factors like your business, trade type, supply chain factors, product mix, lead time, volume vs. variety.
The benchmarking may not give you clarity about all the elements in the benchmarking industry or organization.
Instead, understand your organizational inventory metrics as on today, set it as a baseline and then set a target to reduce it every year.
How should I measure my Inventory?
There are different measures to measure Inventory.
You can measure inventory as a % of sales or you can measure in terms of Inventory Turnover ratio.
Inventory as a % of sales:
In this method, you are measuring your overall inventory value ( RM+WIP+FG) with the sales value.
For example, if overall inventory value is 300 Lakhs and your sales per month is 100 Lakhs , then , you inventory is 300 % of sales.
This measurement is linked with sales, you can always compare with sales and you can relatively compare your performance.
Inventory Turnover ratio:
Another proven method of measuring Inventory is Inventory Turn, which implies your organizational capability of turning Inventory frequently to achieve the sales.
Inventory Turn = Cost of Goods sold / Avg Inventory.
Cost of goods sold = This is the cost to make the goods like raw material cost + manufacturing expenses + any other indirect expenses.
Average Inventory = In a given period, say in a month’s time frame, you can take the average Inventory you are maintaining.
For example, you can add up all the day’s Inventory in a month and divide by the working days. That will give the average Inventory.
Some organization has a practice of taking closing stock or opening stock, but that will be skewed to an extraordinarily high or low value.
For example,
To make an annual sales turnover of 100 lakhs, if you have avg inventory 100 L, Your inventory turn would be 100/ 100 =1
alternatively, for the same sales turnover of 100 lakhs, if you have avg inventory 50 L, Your inventory turn would be 100 / 50 =2
In case, if your avg inventory is 10 L, your inventory turn would be =100/10 = 10
The higher the inventory turn is good indicator of your efficient management of inventory.
If there is a higher inventory turn, that means, with minimal Inventory, you are turning many times to achieve the sales turnover, result in lesser working capital or better cash flow.
Hence, one of the practical measures of Inventory would be ” Inventory Turn.”
Increasing Inventory Turn is possible only when you look into the root causes of the symptoms and initiating strategic and tactic initiatives.
That is a continuous activity, and you need to benchmark yourself and continuously work on optimizing the Inventory without affecting the delivery performance.
Holistic Approach to manage inventory in small business
In most of the organization, Inventory is a concern for the business head.
When we say inventory, it consists of Raw Material *+ Work in Process (WIP)+ Finished Goods Inventory.
* It includes raw material used in product + consumables + spares for equipment also.
Why inventory is a concern ?:
There are three main issues with holding large amounts of stock.
Firstly, it ties up working capital that could be better used elsewhere.
Secondly, high inventory takes up a lot of space and requires more handling and staff deployment.
Thirdly, even with high inventory levels, delivery deadlines may not be met, and holding onto inventory increases inventory costs and manufacturing costs.
From a lean perspective, inventory is considered waste, and merely reducing it is not enough. High inventory levels are merely a symptom, and to reduce or control inventory significantly, the underlying causes need to be addressed.
This requires a holistic approach that manages the entire manufacturing, supply chain, and order procurement processes strategically and tactically.
Given the factors affecting the inventory either in RM stage or WIP stage or FG stage.
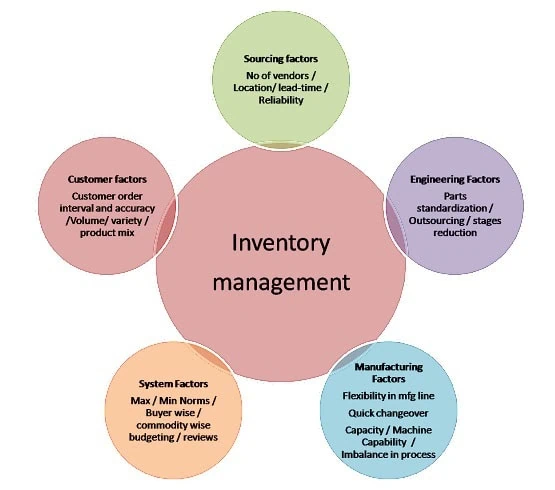
The factors may vary slightly depending upon the industry, but with our experience in many manufacturing industries, the following significant factors should be revisited for better inventory management.
1. Manufacturing factors
2. Engineering factors
3. Supply chain factors
4. Customer factors
5. Internal System factors
Manufacturing factors :
Most of the time, the WIP inventory is primarily based on the lot size, changeover time, machine/plant capacity, reliability of machine/ plant equipment, the overall flexibility of the resources, and the capacity imbalance among the process concerning the customer’s order pace or takt time.
If you want to reduce or control WIP, the above factors must be revisited and re-engineered.
Engineering factors :
It includes the no of parts in the components, standardization among the parts and modular systems, Processes involved in manufacturing those parts and the stages involved in manufacturing either internal or external sources and so on
Supply Chain Factors :
This factor is more of the organization’s strategic intent on the supply chain design. It includes the number of vendors for each part, their location, pricing factors, lead time to supply, the reliability of the vendor base, and so on
Customer Factors :
It is more externally driven. However, management has a choice to drive. It includes the customer profile, either tier 1, tier 2, or OEM, the customer’s location, demand pattern, forecasting accuracy, the number of products or product lines, varieties, and volume in each variety. Those factors govern the inventory of RM+WIP+FG.
Internal system Factors :
Irrespective of external factors and industry type, the discipline and internal management processes govern the inventory to some extent. It includes Norm fixation for each commodity or part, budgeting, buyer accountability fixing, regular reviews, and a management communication system among the team.
The holistic approach of Inventory management is a continuous management effort to balance the delivery and cost.
Software for Inventory Management
Given below some of the software i have witnessed in my client’s operations.
These are just a few options, and many other inventory management software solutions are available on the market.
When choosing the right inventory management software for your small business, it’s essential to evaluate your specific business needs, budget, and integration requirements.
Zoho Inventory:
Zoho Inventory is a cloud-based inventory management solution that offers features such as inventory tracking, order management, purchase management, and integration with other Zoho business apps. It is scalable and offers flexible pricing plans suitable for small businesses.
Tally.ERP 9:
Tally.ERP 9 is a widely used accounting and inventory management software developed by Tally Solutions, an Indian company. It offers inventory management features such as stock tracking, batch-wise inventory tracking, multi-location inventory management, and integration with other business processes.
Odoo’s inventory management
Odoo’s Inventory management module provides features for tracking inventory levels, managing stock movements, handling multiple warehouses and locations, conducting inventory adjustments, and integrating with other business processes such as sales and purchasing. It also offers barcode scanning functionality for efficient inventory management operations.
The above list is not a recommendation from me,but they are popular and widely used in many small business in India. You need to do research for right software and vendor .
Factors to be considered for choosing a right inventory management software
Stock Tracking: Tracking capability of inventory levels accurately including details like stock quantity, batch numbers, expiry dates, and stock locations.
Inventory Control: Software should allow businesses to exercise control over their inventory by setting reorder levels, defining stock groups and categories, managing stock transfers, and performing stock reconciliation.
Multiple Units of Measure: Software must support multiple units of measure (UOM) for items, enabling businesses to manage inventory in various units based on their purchasing and selling requirements.
GST Compliance: With India’s Goods and Services Tax (GST) system compatibility and help the business manage their inventory, in compliance with GST regulations, including generating GST-compliant invoices, filing GST returns, and maintaining accurate GST records.
Integration feasibility: Software should seamlessly integrate inventory management with other business processes such as accounting, sales, and purchasing, providing a holistic view of the business operations.
Reporting and Analysis: The software must offer customizable inventory reports and analytics tools to help businesses gain insights into their inventory performance, identify trends, and make informed decisions.
Overall the software must be user friendly, customized to your business and ease of integration with other functional modules in the future.
should we go for standalone inventory management software or holistic ERP software to manage inventory?
Standalone Inventory Management Software:
Standalone inventory management software is specialized software that offers features tailored for inventory management tasks.
If inventory management is your primary concern and you don’t need additional modules like accounting or HR management, standalone software might be a better fit for you.
One of the benefits of standalone inventory management software is that it has quicker implementation times compared to full-scale ERP systems. This can be beneficial if you need to get your inventory management system up and running rapidly without the complexities of implementing an entire ERP solution.
Another advantage of standalone inventory management software is that it may be more cost-effective, particularly for smaller businesses with limited budgets. You only pay for the features you need, without the additional costs associated with an ERP suite.
However, it’s important to note that some standalone inventory management solutions may lack scalability, especially if your business grows or if you need to integrate additional functionalities in the future.
Therefore, it’s crucial to ensure that the standalone software you choose can accommodate your future needs.
Holistic ERP Software:
An ERP software offers a fully integrated solution that combines inventory management with other essential business functions such as accounting, sales, purchasing, HR, and more. This integration provides a seamless flow of data across different departments, reducing redundancy and improving efficiency.
With ERP software, you get a holistic view of your entire business operations, not just inventory. This comprehensive visibility allows for better decision-making, as you can analyze data from various departments in real-time.
ERP systems streamline business processes by automating repetitive tasks and providing standardized workflows.
This can lead to improved productivity and reduced manual errors.
Investing in an ERP system provides room for growth and scalability.
As your business expands, you can easily add new modules and functionalities to the existing ERP framework without the need for significant changes or integrations.
In conclusion,
standalone inventory management software might be suitable if inventory management is your primary concern and you have budget constraints or specific requirements.
However, if you’re looking for a comprehensive solution that integrates inventory management with other business functions and provides scalability for future growth, holistic ERP software may be the better option.
It’s essential to evaluate your business needs carefully and choose a solution that aligns with your long-term goals